How We Serve Steel Industry & Reheat Furnace Operators
The steel industry is under constant pressure to ensure that quality products are produced, while remaining price competitive. However, oftentimes reheat furnaces are not operating as efficiently as pThe steel industry is under constant pressure to ensure that quality products are produced, while remaining price competitive. However, oftentimes reheat furnaces are not operating as efficiently as possible, having significant adverse effects on product quality and operating costs. Steel manufacturers and others operating reheat furnaces can leverage AI to optimize their furnaces to reduce fuel costs and operating expenses.
While there are many different types and designs of reheat furnaces, they all face common challenges such as inefficient energy usage, low granularity or difficult to use control systems, and higher than desired reject rates due to unacceptable slab temperatures after extraction.
Some of the difficulties in achieving the desired operating characteristics for reheat furnacescan be attributed but are not limited to:
• Diverse product types often adjacent to each other in the furnace
• Inconsistent burner performance and unstable flame location
• Limited temperature feedback from inside the furnace
• Process unpredictability such as delays for maintenance and other issues
• Generally poor correlation between temperature setpoints and measured temperatures in the furnace
• Furnace degradation leading to heat loss and difficulty meeting temperature setpoints
Why Griffin’s AI Toolkit?
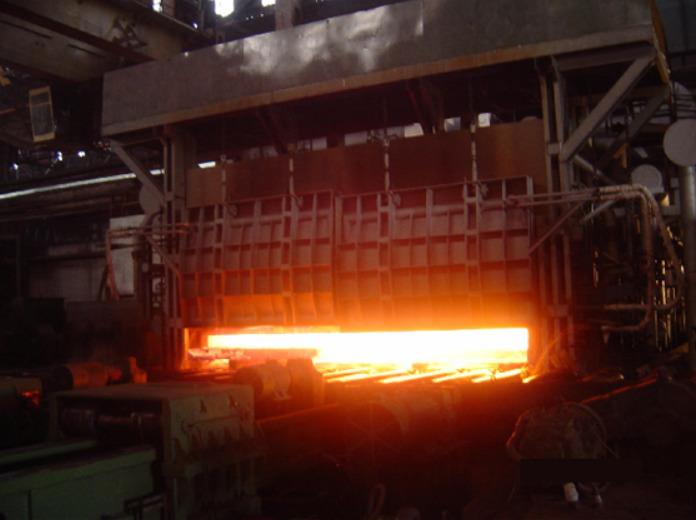
The Griffin AI Toolkit offers those in the steel industry a no-code graphical user interface with a number of tools for modeling and analyzing existing processes. We also provide the functionality to control and optimize those processes in real-time with minimal PLC or DCS reprogramming. The Griffin AI Toolkit provides the benefits of AI-enhanced GUI-based control which can be quickly realized across multiple sectors of steel production, such as PID process control, metallurgical modeling and optimization, reheat and blast furnace control, and more. Implementations can save millions of dollars in fuel and operating costs associated with production.
At a large Midwestern steel production facility, Griffin is being used to determine optimal temperature setpoints for a group of reheat furnaces as they process a mix of material with differing temperature requirements. By building a digital twin of the reheat process and creating an informative new graphical display, operators are given access to a more informative view of the heating progress of slabs. A time-sensitive neural network model is used to predict the rolling temperature of slabs and adjust furnace temperatures to meet production requirements. Griffin also automates other operator tasks, such as creating heating delays when necessary in order to prevent temperature-rejected material, which was reduced to virtually nil as a result of the project.
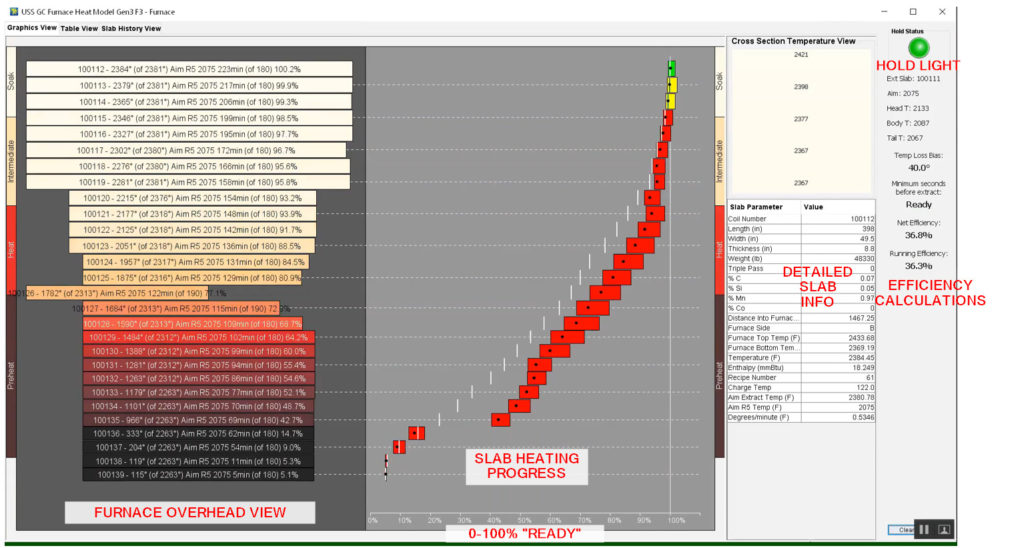
Contact us to learn how the Griffin Toolkit can help optimize your reheat furnace to increase productivity and reduce fuel consumption and costs.